Nowoczesne metody projektowania układów elektrycznych w przemyśle
Dostarczenie zasilania do hal produkcyjnych i działających w nich urządzeń może być wyzwaniem. Z pomocą przychodzą specjaliści oraz nowoczesne narzędzia i techniki, a w tym oprogramowanie CAD/CAE i symulacja komputerowa układów elektrycznych. Dowiedz się więcej o tym, jak dziś projektuje się elektrykę dla zakładów przemysłowych i w jaki sposób dobiera się najlepsze rozwiązania dotyczące zasilania dla konkretnych przedsiębiorstw.
Oprogramowanie CAD/CAE – niezbędne narzędzie do projektowania elektryki dla przemysłu
W nowoczesnym projektowaniu sieci elektrycznych tak samo ważne są umiejętności i wiedza specjalistów jak rodzaj wykorzystywanych przez nich narzędzi. Dziś inżynierowie mają do dyspozycji CAE, czyli Computer Aided Engineering (tłum. z ang. inżynieria wspierana komputerowo).
CAE to oprogramowanie, które pomaga inżynierom w szeroko pojętym projektowaniu wyrobów. Za jego pomocą specjalista może tworzyć całe procesy technologiczne, a także wykonywać skomplikowane obliczenia i zaawansowane analizy techniczne. Oprogramowanie CAD/CAE umożliwia również projektowanie obwodów drukowanych oraz symulację działania układów elektrycznych. Jego funkcjonalność oznacza zarówno korzyści dla inwestora, jak i możliwość precyzyjnego stworzenie elektryki przemysłowej dla inżyniera.
Czym dokładnie jest oprogramowanie CAD?
CAD – Computer Aided Design – to komputerowe wspomaganie projektowania. Umożliwia ono tworzenie projektów w przestrzeni wirtualnej. Za jego pomocą inżynier może przygotować zarówno projekty 2D, jak i 3D. Oprogramowanie CAD wykorzystuje się w wielu branżach i znalazło ono zastosowanie również podczas tworzenia planów obwodów elektrycznych.
CAD pozwala zarówno na projektowanie elektryki, jak i na tworzenie całej dokumentacji projektowej. Korzystający z tego oprogramowania inżynier ma do dyspozycji biblioteki symboli i komponentów oraz moduły do tworzenia rysunków 2D. Narzędzia CAD umożliwiają automatyczne wypełnianie parametrów zawartych w założeniach projektu. Za ich pomocą inżynierowie mogą tworzyć własne szablony dokumentacji – w taki sposób, aby były one dostosowane do standardów obowiązujących w przedsiębiorstwie.
Jakie zalety wiążą się z korzystaniem z oprogramowania CAD/CAE?
Oprogramowanie CAD/CAE to nowa jakość w projektowaniu układów elektrycznych. Jest ono dziś niemal niezbędne w przypadku tworzenia rozbudowanych schematów elektryki dla zakładów przemysłowych, gdzie dostęp do zasilania musi mieć wiele maszyn, które charakteryzują różne parametry dotyczące poboru energii.
Symulacja komputerowa układów elektrycznych – niższe koszty dla inwestora
Aby ocenić, czy dany układ elektryczny będzie sprawdzał się na hali produkcyjnej lub w parku maszynowym, wcześniej trzeba było przekonać się o tym w praktyce. Jednak jeżeli jego pewne elementy zaczynały szwankować, okazywały się źle dopasowane, oznaczało to konieczność kosztownej korekty sieci zasilania czy naprawy usterek. Między innymi po to, aby tego uniknąć, wykorzystuje się oprogramowanie CAD/CAE.
Dzięki temu, że za jego pomocą można zarówno przeprowadzać symulację działania układów elektrycznych, jak i wykonywać niezbędne obliczenia, ryzyko błędu jest ograniczone do minimum. Projekt sieci elektrycznej w zakładzie przemysłowym jest ściśle dostosowany zarówno do parametrów urządzeń tworzących np. taśmy produkcyjne, jak i do specyfiki samego budynku. Dlatego wykorzystanie oprogramowania CAD/CAE to sposób na stworzenie sprawnie i bezawaryjnie działającego układu elektryki – takiego, który nie będzie wymagać korekty lub w jeszcze dalszej perspektywie drogiej szybkiej naprawy.
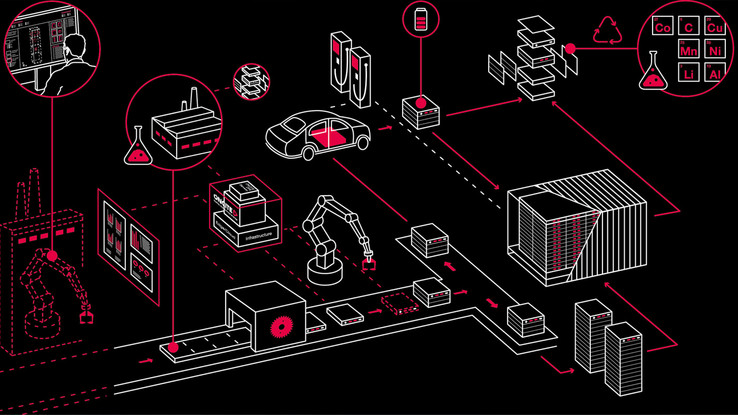
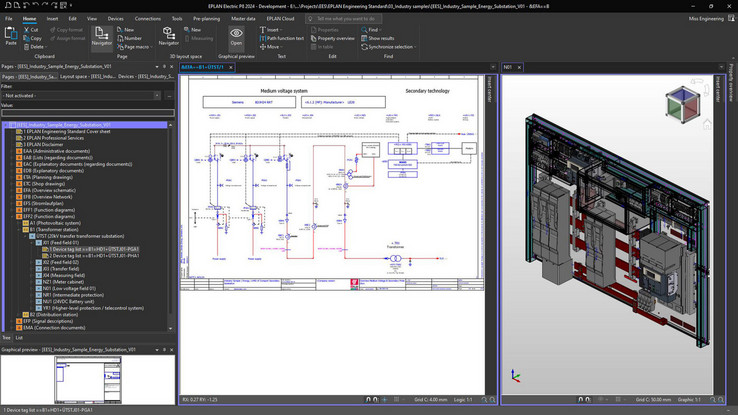
Automatyzacja projektowania elektrycznego – szybciej realizowane inwestycje
Mimo że za stworzenie układu elektrycznego odpowiada inżynier i nie ma mowy o tym, aby bez jego udziału mógł powstać projekt, to wiele automatycznych zadań może powierzyć on oprogramowaniu CAD/CAE.
Wykonywaniem obliczeń i pragmatycznych analiz może zająć się komputer. Oprócz tego nie ma potrzeby czasochłonnego i kosztownego tworzenia prototypów układów elektrycznych. Powstają one i są skrupulatnie testowane w środowisku wirtualnym. Oznacza to skrócenie czasu produkcji gotowego wyrobu – w tym przypadku elektryki zasilającej zakład przemysłowy.
Czym jest inżynieria odwrotna w elektronice?
Bywa, że w zakładzie elektrycznym znajduje się już sieć elektryczna, która do tej pory spełniała swoje zadanie. Jednak wraz z rozwojem przedsiębiorstwa mogło okazać się, że przestała ona wystarczać, w związku z czym wymaga modernizacji. Polepszenie parametrów sieci elektrycznej czy jej rozbudowa to zawsze wyzwanie, ale w niektórych przypadkach jest to szczególnie skomplikowane przedsięwzięcie – wtedy z pomocą przychodzi inżynieria odwrotna. Jest ona wykorzystywana także w przypadku pojedynczych urządzeń elektronicznych, które wymagają modernizacji lub naprawy.
Inżynierię odwrotną nazywa się także techniką odwracania lub programowaniem zwrotnym. Metodę tę wykorzystuje się, gdy np.:
- trzeba zmodernizować układ elektryczny, którego całość lub poszczególne elementy nie mają dokumentacji technicznej CAD;
- trzeba zbudować nieistniejące obecnie cyfrowe archiwum lub tworzenia wirtualnego środowiska do wykorzystania w przyszłości,
- części zamienne układów elektrycznych, które uległy awarii, nie są już dostępne u producenta.
Inżynieria odwrotna w elektronice to inżynieria “od tyłu”. Inżynier ma już gotowy wyrób, a jego zadaniem jest odtworzenie budowy, schematu działania, a dopiero potem jego naprawa lub modernizacja. Taki proces techniczny znajduje zastosowanie zarówno w przypadku układów elektronicznych, jak i rozbudowanych sieci elektrycznych w zakładach przemysłowych.
Na czym polega zastosowanie algorytmów genetycznych w projektowaniu elektryki?
Algorytm genetyczny słusznie może kojarzyć się z doborem naturalnym i poszukiwaniem odpowiedniego genomu. Okazuje się jednak, że ten specyficzny ciąg jasno zdefiniowanych czynności można wykorzystywać także z układami FPGA (field-programmable gate arrays).
FPGA to układy, które można przeprogramowywać bez ich demontażu. Składają się one z chipów, które można szybko programować, aby zmienić parametry układu elektrycznego. FPGA da się cały czas kontrolować i testować. Jest to możliwe, gdyż wszystkie informacje o ich parametrach znajdują się w chipach, a ich wartości są mierzone w czasie rzeczywistym. Natomiast same chipy-regulatory można udoskonalać i badać dzięki zastosowaniu algorytmów genetycznych.
Układy elektryczne to rodzaj ogromnej populacji. Aby zbadać “genotyp” ich wszystkich, potrzeba bardzo dużej mocy obliczeniowej – takiej, jakiej nie mają jeszcze dzisiejsze komputery. Jednak zastosowanie algorytmów genetycznych w dziedzinie elektryki to nowoczesny kierunek rozwoju tej branży. Taka technologia pozwala tworzyć jeszcze wydajniejsze i lepiej przystosowane do wymagań użytkowników układy elektryczne. Algorytmy genetyczne pomagają inżynierom rozwiązywać problemy i znajdować odpowiedzi na trudne pytania, dzięki czemu powstają coraz doskonalsze sieci zasilania w zakładach przemysłowych.
Na czym jeszcze polega nowoczesne projektowanie układów elektrycznych w przemyśle?
Innowacje w dziedzinie energoelektroniki to sposób na to, by powstawały układy elektryczne i elektroniczne jeszcze lepiej dopasowane do rosnących wymagań zakładów przemysłowych. Inżynierowie, aby sprostać oczekiwaniom inwestorów, ciągle poszukują nowych rozwiązań. Układy elektryczne w przemyśle spożywczym, przetwórczym czy samochodowym muszą nadążać za dynamicznymi zmianami, jeżeli chodzi o zapotrzebowanie energetyczne maszyn znajdujących się w zakładach. Z pomocą przychodzi CAD/CAE i inne innowacje.
Należy do nich również integracja systemów elektrycznych. Polega ona na takim projektowaniu układów, aby ich poszczególne komponenty mogły jak najlepiej się ze sobą „komunikować”. Pozwala to na stworzenie wydajniejszego i zwykle oszczędniejszego zasilania.
Bezawaryjne i funkcjonalnie zaprojektowane układy zasilania to jeden z fundamentów działalności zakładów przemysłowego. Nowoczesna inżyniera elektryczna i Innowacyjne rozwiązania z zakresu elektryki i energetyki pozwalają wydajnie i możliwie najoszczędniej dostarczać zasilanie do taśm produkcyjnych czy całych parków maszynowych. Przekłada się to na rentowność całego przedsiębiorstwa.